Alfa Laval printed circuit heat exchangers (PCHEs) combine superior robustness and integrity with an exceptionally high heat transfer rate, in a unit that’s up to 85 % smaller and lighter than comparable shell-and-tube exchangers. The unique design results in excellent performance, lower installation and operational costs, as well as improved safety. Each unit is also fully customizable according to your exact needs.

First-class efficiency with the smallest possible footprint
-
All-stainless-steel construction, fully customizable to match the duty position and application required
-
Robust design handles pressures up to 1000 barg (14,500 psi) and temperatures ranging from -196°C (-320°F) to 800°C (1472°F)
-
Allows 1°C approach temperatures within your process
-
Immune to the effects of fluid pressure pulsations and fluid flow induced vibration
-
Fully compliant with ASME Boiler & Pressure Vessel Code (Section VIII, Division 1 with U Certification Mark) and CE Marking (as per PED 2014/68/EU)
Alfa Laval printed circuit heat exchangers are an ultra-compact solution for improving sustainability in marine, energy and oil & gas applications. Photo-chemically etched fluid channels provide exceptionally high thermal performance, while state-of-the-art diffusion bonding produces a solid core packed with heat transfer area. The combined result is maximum efficiency and minimum footprint, ensuring the lowest total lifecycle cost.
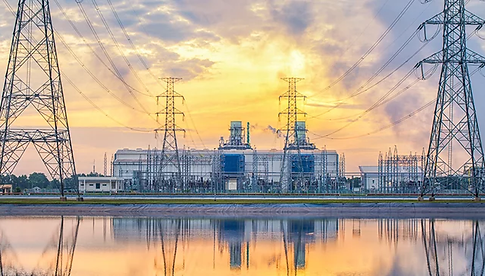
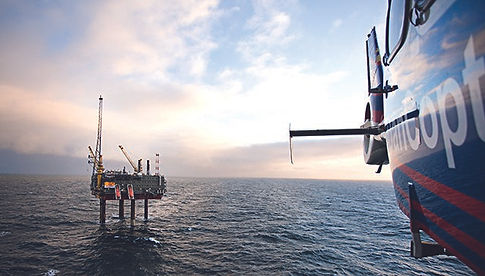
Applications
Technical data
Alfa Laval printed circuit heat exchangers are designed specifically to deliver unparalleled compactness and efficiency in clean and high-pressure duties that are beyond the capability of other welded plate type heat exchangers. The robust design can reliably handle pressures ranging from vacuum to 1000 barg (14,500 psig).
Typical marine applications include high-pressure vaporization in fuel gas supply systems (FGSS), LNG regasification on FSRU and SRV™ vessels. In the energy sector, printed circuit exchangers are used in gas processing and cryogenic LNG applications. Typically, these are gas compression systems offshore, hydrocarbon gas and water dew-pointing. In LNG, where high energy recovery is desired, they are used in End Flash Gas and BOG handling systems. They can also be found in turbine fuel gas preheating and supercritical carbon dioxide (sCO2) applications for power generation.
Design pressure
CE/PED Vacuum to 1000 barg (14,500 psig)
ASME Vacuum to 1000 barg (14,500 psig)
Design temperature
316/316L SST –196°C (cryogenic) to 800 °C (–321°F to 1,472 °F)
Connections
2–30 inch typical, customizable
Standard materials
316L SST (other materials available on request)
Dimensions/Weights
On request, tailored towards requirements ranging from a few kilograms to tens of tons
-
Alfa Laval welded heat exchangers maximize energy efficiency and heat recovery, with innovations that deliver exceptional thermal performance and reliability, for a wide range of duties. But it’s more than technology. It’s also the people: experienced experts with deep process knowledge and a global service presence. Combined, that’s how you improve sustainability.
How it works

Working principle
Printed circuit heat exchangers operate with two or more media on opposite sides of a bonded plate. It is possible to have high-pressure flows on both sides, and a 2D or 3D plate pattern can be optimized to provide the required thermal length and pressure drop.
The printed circuit heat exchanger design has a complex flow pattern chemically etched on flat sheets of material. This flow pattern is optimized for each specific customer duty to provide the required thermal and hydraulic characteristics. Each flow circuit plate pattern can be different, giving the possibility of asymmetric flows and optimized 2-phase behaviour. The individual plates are then stacked into a block and diffusion bonded in a state-of-the art furnace at high temperature and pressure. Multiple blocks can be welded together to create the required thermal capacity or heat transfer area. Inlet and outlet flow manifolds, customer connections and (if required) connections for drain, ventilation or cleaning are welded onto the completed core to finalize the heat exchanger. Design pressures of up to 1000 barg (14,500 psiG) in 316L SST are achievable with this configuration. Heat transfer surface areas are tailored based on requirements.
Design
Improving sustainability with welded solutions from Alfa Laval
-
Alfa Laval welded heat exchangers maximize energy efficiency and heat recovery, with innovations that deliver exceptional thermal performance and reliability, for a wide range of duties. But it’s more than technology. It’s also the people: experienced experts with deep process knowledge and a global service presence. Combined, that’s how you improve sustainability.
Unique features that make the difference
Alfa Laval has more than 80 years’ experience in heat transfer technology, and we are continuously developing new innovations to improve the performance, reliability and sustainable impact of our equipment. Our printed circuit heat exchangers include a number of unique features you won’t find anywhere else:

OptiBond™
A robust and compact solution for high-pressure needs
State-of-the-art diffusion bonding technology provides the highest durability and thermal efficiency within an ultra-compact welded plate heat exchanger.

3DPlate™
Prevents clogging under freezing conditions
A patented 3D plate pattern maintains high efficiency and maximum uptime when using water-based fluids like glycols in cryogenic applications.